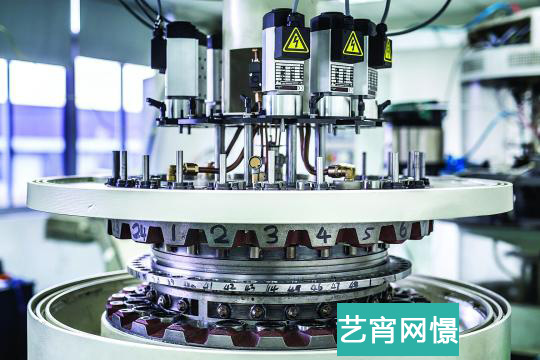
●真彩文具研发的国内第一台能够生产圆珠笔钢珠的机器。

●真彩文具工人参与研发的圆珠笔芯测试仪。

●真彩文具创始人、董事长黄小喜定期到位于江苏昆山的车间监督生产。
“我们还不具备生产模具钢的能力,包括圆珠笔头上的‘圆珠’,目前仍然需要进口。这都需要调整结构。”2016年的第一个工作日,国务院总理李克强在太原主持召开钢铁煤炭行业化解过剩产能、实现脱困发展座谈会。会上,李克强总理以平时大家所用的笔尖上的那颗小小“圆珠”为例,亮出了中国制造与世界一流选手之间不小的差距。
确实,中国是制笔大国,但不是制笔强国,我国的制笔企业很多集中在笔杆生产组装产业链的低端,而笔头油墨等关键部件,特别是精密制笔机械等关键设备依赖进口。
2005年起,广东省政协委员、真彩文具股份有限公司(下简称“真彩文具”)董事长黄小喜,就带领他公司的团队,埋头攻克这个难题。2014年,真彩文具自主研发的笔头多工位加工机床最终通过了科技部的验收。
黄小喜说,“从我们研发出拳头产品‘真彩009中性笔’那一天起,我就一直有个信念,一定要造出真正的国产笔头。”
曾经挑战失败的笔尖难题
“你不要看笔尖只有那么一点点,里面包含的工艺技术非常复杂,实际上,我们国家在上个世纪90年代就曾经想研制过国产笔尖。”黄小喜说,当时,国家轻工部也曾拨款好几百万元立项,由北京某军工研究院和上海某圆珠笔厂共同承担笔头装备的研发工作,但最终以失败告终。
“笔尖难题”困扰业内已久。作为国内引进中性笔第一人,黄小喜自1989年就一头扎进制笔行业,专门找到了上述项目的总设计师,认真搜集了曾经的研制信息。“当时不太成熟的地方有几个。首先,瑞士的笔尖生产设备当时刚推出不久,本身就还不太稳定。另一个原因就是只是将设备买回来进行拷贝,而没有认真去研究里面的设计理念是什么,加上当时国内缺乏制造、检测如此高精度零件的工作母机……”
汲取曾经的教训,黄小喜从2005年起几次带队前往瑞士,与多年合作伙伴米克朗公司的机械专家面对面探讨。“了解人家的设计理念非常关键,为什么人家可以做到100分,而我们的模仿往往只能做到80分,就是没有搞清楚人家为什么要这么设计。”
屡试屡败也要让设备国产化
即便有备而来,但笔尖设备的国产化之路依然比想象中的要难得多。
“这套装备最难的地方是要把精度、高速和长期稳定性结合起来。”真彩文具副总经理陆宪明说,笔尖装备一旦启用就是24小时不间断工作,对材料的稳定性要求非常高。“原机上有些材料甚至是国内没有的,我们只能是通过大量的实验,寻找能够达到要求的合适材料。”
“任何零件只要相互贴合,时间长了一定会产生不同程度的磨损。对笔头制造等高精度设备来说,这种磨损是致命的。但瑞士米克朗将整个加工托盘依靠气压托起来。”于是,真彩花大价钱进口了设备,拆解开来,再将自己研发的子系统替换上去,对照运转效果找出问题所在,再研发、再改善、再替换……
几千万资金花出去,却迟迟无法取得想要的成效,整个团队一度想放弃,“也有人来劝我。”黄小喜回忆说,“可做这台机器对于我来说,就像是一个信念一样,我还是希望能把它做成。”
“如果单说只是为了赚钱,其实我们做不做这个都不是关键,可对于一个制笔人,做一台国产笔尖设备,这就如同一个理想。人还是需要一点理想。”
自主研发令一支笔省四五分钱
关键时刻,科技部的项目推了黄小喜一把。
2011年两会期间,有调研组提交了两份调研报告,其中“我国每年生产380亿支圆珠笔,但笔头近90%来自进口”的数据,引起了国家领导人的注意。经批示,当年两会结束后,科技部紧急启动了“制笔行业关键材料及制备技术研发与产业化”的专项课题。作为行业领头羊,真彩文具主动承担了其中“高精度多工位笔头加工机床”和“中性墨水关键技术开发与产业化”两个关键课题。
2014年,真彩文具自主研发的笔头加工机床样机终于通过了科技部验收。在研发过程中,其中多项替代技术甚至“青出于蓝而胜于蓝”———进口机床使用的P LC控制系统,被更为先进的数控系统所取代;进口机床电机1 .5万转的最高转速,也被提高到6万转,相当于每个加工位的效率提高了4倍……而这台国产机的成本仅为进口机的1/3.
不仅仅是设备,现在真彩文具使用的是自主研发的机床、材料和墨水。由此,真彩每生产一支零售价为一块多钱的笔,制造成本就会降低四五分钱。真彩文具每天生产几百万支笔和笔芯,成本就能降低几十万元,一年下来就是六七千万元,经济效益非常可观。
虽然做出了国产笔头,但黄小喜也知道,远还没有到完美的程度。“预计5年后,我们使用国产圆珠笔笔头产量有望提高到总产量的80%,进而全面替代进口机器和原材料。”黄小喜说,真彩文具自主生产的设备还在不断升级改造中,但现在的自己非常有信心,下一步,真彩文具能将机器做得越来越好。